The development and application of innovative approaches for surface engineering and coating based on beam and plasma techniques often require dedicated beam and plasma sources, e.g. broad beam ion sources for reactive ion beam etching, plasma jets and laser-induced plasma sources for reactive etching processes at atmospheric pressure as well as metal and gas plasma sources for thin film deposition. These sources which represent the “tool kit” of the IOM are developed and optimized at the Institute, securing one of the foundations of the island position of the IOM in this field of technology. Part of the development of broad beam ion sources is devoted to electric propulsion for space applications. In addition, electron sources for charge neutralization of ion beams as well as electrical components for operating beam sources are being developed too.
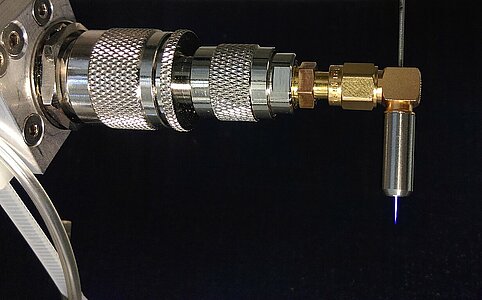
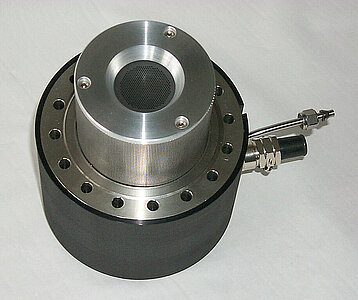
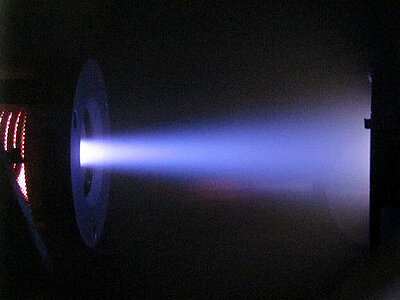
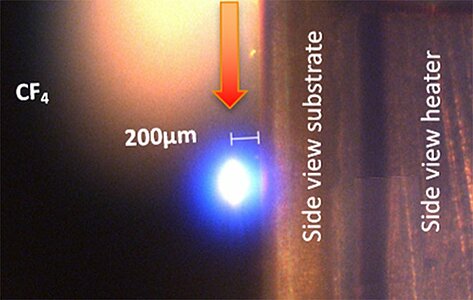
Expertise
- Development and optimization of broad beam ion sources, for example, for reactive ion beam etching and electric propulsion systems
- Development and optimization of atmospheric plasma jet sources, for example, for ultra-precise ion beam figuring of optical elements
- Development and optimization of metal and gas plasma sources for thin film deposition
- Development and optimization of laser-induced plasma sources for engineering surfaces at atmospheric pressure
Highlights
Vorrichtung zur Erzeugung eines Plasma- oder Radikalstrahles
G. Böhm, T. Arnold, H. Paetzelt
Gebrauchsmuster DE 202017103165 U1 (2017), DPMA
GebrauchsmusterschriftThe invention comprises a device for generating a plasma or radical beam by exciting a gas stream of suitable composition by means of pulsed high-frequency energy. This source can, for example, be used for plasma machining of surfaces using atmospheric plasma processes.
Human health risk evaluation of a microwave-driven atmospheric plasma jet as medical device
A. Lehmann, F. Pietag, Th. Arnold
Clin. Plasma Med. 7-8 (2017) 16-23
DOI: 10.1016/j.cpme.2017.06.001The aim of this study was the characterisation of a microwave-driven atmospheric plasma jet (APJ) dedicated for medical applications. The scientific focus includes harmless sterilization of surfaces and therapeutic treatments in dentistry. The plasma was investigated with respect to potential health risks for human beings, which could occur especially due to the gas temperature, heat flow, patient leakage current, UV emission and ozone emission from the plasma jet. The results of the experiments indicate a high potential of the plasma jet to be used as a medical device exhibiting low gas temperatures up to 34 °C. The investigated APJ exhibits physical properties that might not constitute health risks to humans, e.g. during treatment in dentistry.
Laser-Induced reactive microplasma for etching of fused silica
M. Ehrhardt, P. Lorenz, B. Han, K. Zimmer
Appl. Phys. A 126 (2020) 842
DOI: 10.1007/s00339-020-04019-xThe ultra-precise machining (UPM) of surfaces with contact-free, beam-based technologies enables the development of flexible and reliable fabrication methods by non-vacuum processes for future application in advanced industrial fields. Laser machining by laser ablation features limitations for ultra-precise machining due to the depth precision, the surface morphology, and laser-induced defect formation. Contrary to physically based etching, chemically based dry and wet processing offer high quality, low damage material removal. In order to take advantage of both principles, a combined laser-plasma process is introduced. Ultra-short laser pulses are used to induce a free-standing microplasma in a CF4 gas atmosphere due to an optical breakdown. CF4 gas, with a pressure of 800–900 mbar, is ionized only near the focal point and reactive species are generated therein. Reactive species of the laser-induced microplasma can interact with the surface atoms of the target material forming volatile products. The release of these products is enhanced by the pulsed, laser-induced plasma resulting in material etching. In the present study, SiO2 surfaces were etched with reactive species of CF4 microplasma generated by their laser-induced break down with 775 nm pulses of an fs-laser (150 fs) at a repetition rate of 1 kHz. The dependency of the depth, the width, and the morphology of the etching pits were analysed systematically against the process parameters used. In particular, a linear increase of the etching depth up to 10 μm was achieved. The etched surface appears smooth without visible cracks, defects, or LIPSS (Laser-induced periodic surface structures).
Design and performance test of a RF plasma bridge neutraliser
F. Scholze, D. Spemann, D. Feili
Proc. 36th Int. Electric Propulsion Conference (IEPC), IEPC-2019-475 (2019)Most electric propulsion concepts require electron sources for neutralization of the positive space charge generated by the emitted ion beam. As an alternative to, for example, hollow cathode systems, a radio-frequency plasma bridge neutralizer (RFPBN) employing an inductive-coupled plasma excitation was designed and tested at the Leibniz Institute of Surface Engineering (IOM). The RFPBN concept device consists of a cylindrical plasma chamber and an integrated matching network for a fixed frequency of 13.56 MHz and is adapted for applications which require electron currents between 2 and 100 mA. The neutralizer performance as the relation between extracted electron current and supplied DC and RF power shows that the presented concept is a viable alternative to conventional electron sources for ion beam neutralization. The RFPBN device was also successfully tested to withstand the mechanical stress regarding vibration and shock imposed by a typical space mission. Furthermore, the RFPBN successfully passed a 900 hour endurance test and an 100 hour neutralization verification test using a RIT10 EVO gridded ion thruster from ArianeGroup.
IonJet - Engineering Model of a low-cost electric propulsion system for small satellites
F. Scholze, F. Pietag, H. Adirim, M. Kreil, M. Kron, R. Woyciechowski, C. Bundesmann, D. Spemann
Development and test of a cost-efficient gridded ion thruster propulsion system for small satellites – IonJet
J. Electric Propulsion 1 (2022) 28
DOI: 10.1007/s44205-022-00028-5Within the DLR-funded joint project IonJet of IOM and Aerospace Innovation GmbH, an engineering model of a low-cost electric propulsion system for small satellites was developed. Whereas the flow control subsystem is based on the MICROJET 2000 system launched 2016 on the BIROS satellite, the thruster subsystem is based on a novel patent-pending gridded ion thruster where the neutralizer is integrated in the ion thruster allowing for simultaneous ion and electron extraction. This design allows reducing the number of components and consequently costs and system complexity. The entire system was successfully tested under vacuum conditions regarding ignition and stable operation of the propulsion system. In the performance tests, thrusts of 1 mN could be achieved using Xenon gas as propellant at a total power consumption of less than 50 W as well as specific impulses larger than 1000 s, including the gas consumption of the neutralizer. In addition, first tests with Krypton gas were performed showing that for the same total power the achievable thrust is reduced to 55% – 68% of that for Xenon.